This article is published in Aviation Week & Space Technology and is free to read until Nov 21, 2024. If you want to read more articles from this publication, please click the link to subscribe.
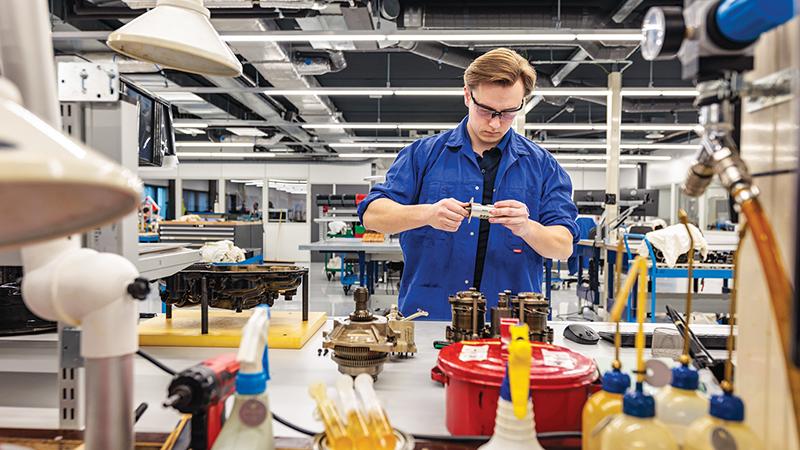
Fokker has doubled the size of its integrated drive generator shop at Amsterdam Airport Schiphol.
Fokker Services Group has been on a growth and transformation path over the past three years, boosting its MRO capabilities, expanding its global facilities and implementing digitalization and sustainability strategies.
Following the 2021 acquisition of Fokker Services and Fokker Techniek and the businesses’ 2022 rebranding to Fokker Services Group (FSG), co-CEOs Roland van Dijk and Menzo van der Beek have worked to approximately double the company’s size. FSG has doubled its revenue and grown its global staff to over 1,000, up from around 500 at the time of the acquisition.
According to van Dijk, the pair sought to expand customer relationships as a driver for building up new capabilities. “[The existing customer relationships] were just a little bit underutilized and undermanaged, so we’ve worked on that side and the capability side,” he tells Inside MRO. “There was a lot of knowledge and a lot of things that we could build further.”
At MRO Asia-Pacific in September, Fokker Services Asia signed a contract to become an authorized service center for Embraer. Earlier this year, Fokker Services America rolled out integrated drive generator (IDG) capability and upgraded its facilities with solar power. Last year, FSG opened a new widebody hangar at Woensdrecht Air Base in the Netherlands that also features solar power and a geothermal energy system.
Facility Revamps
At Amsterdam Schiphol Airport, FSG has been upgrading its facilities to expand its repair shops, implementing new equipment, technology and design features to boost capacity and improve the environment for staff. One of the first to receive a makeover was the IDG shop, which FSG doubled in size at the beginning of this year. The shop is currently repairing around 60 IDGs a month, and FSG wants to grow this capacity by double digits year-over-year.
Van der Beek says IDG capabilities were one of FSG’s first investments beyond Fokker aircraft platforms, and in the past few years demand for those services has grown significantly. The decision to build an IDG shop in the U.S. was driven by both demand for more services and customer considerations around sustainability and nearshoring. “We are confident that if we build capability, [customers] are willing to send business there, so we have more or less upfront commitments,” he says. “That will be an easy step up for that dual capability, and for the future road map, probably more duplication of capabilities will come forward, especially if we are able to create more volume on fewer part numbers.”
To make space for the Schiphol IDG shop expansion, FSG relocated a mechanical shop and centralized all logistics activities at its nearby Hoofddorp warehouse. “It was one big puzzle,” says Dirk Hanenberg, FSG’s director of component services, noting that the facility’s projects are using a phased approach to minimize disruption to other repair work there. “We basically had to free up some space, deploy the new setting and then go to the next phase of the reconstruction.”
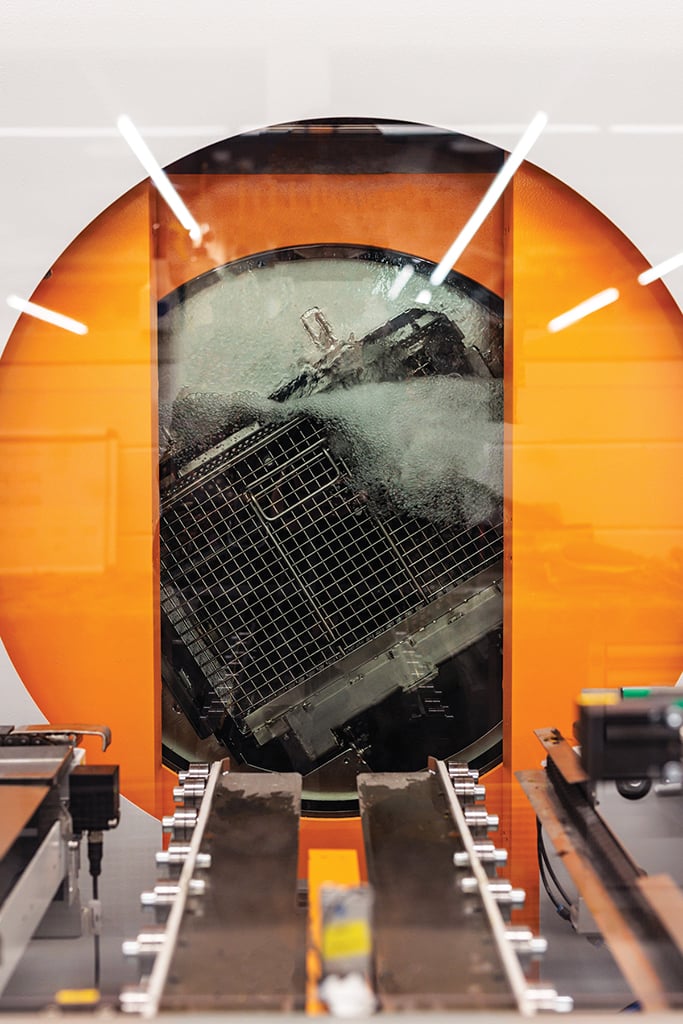
The expanded IDG shop includes more test benches and an automated machine that cleans IDG housings and piece parts. Hanenberg says automation has made cleaning faster and more consistent while also benefiting employee health and the environment, since workers are no longer exposed to chemicals and the self-contained machine reuses 95% of the liquids and solvents involved.
To improve staff experience further, the shop design maximizes natural light, with work benches close to windows and machines in darker corners. The Schiphol shop is working with FSG’s Americas facility in LaGrange, Georgia, to share best practices as that location ramps up its own IDG shop.
“Because we are in different parts of the world, we are increasingly using our scale—not just from one location but also what we learn from other locations—to build efficiency,” says van Dijk.
FSG is also expanding its Schiphol avionics shop, including new automated test equipment to support the Boeing 737 nose-to-tail program the company launched last year with Spanish airline AlbaStar.
The Schiphol facility’s warehouse area was also recently upgraded as part of efforts to improve efficiency. FSG invested in several new technologies, including vertical storage units and a system that allows operators to pick parts for multiple job cards simultaneously. The warehouse also features a pneumatic tube system for AOG part picks that propels required piece parts directly to the repair shop where they are needed. Hanenberg says it previously took an average of 7 min. to deliver parts for every AOG pick; the new system has reduced this to roughly 10 sec.
FSG has similar automation at its Hoofddorp warehouse, including Kardex vertical lift systems, automated parts conveyor belts and new digital processes to handle documentation.
“We’re just trying to make the whole process more digital, step by step, so pictures are automatically uploaded to minimize the human part of handling stuff,” says Franck Scherer, director of material services. “Compared to what it used to be a couple years ago, it’s already well transformed, but there are still ideas and continuous improvement to bring. A lot of [employees] are coming with their own ideas as well, saying, ‘Can we do this to make my life a little bit faster and easier?’ It’s a never-ending process of how to improve the flow.”
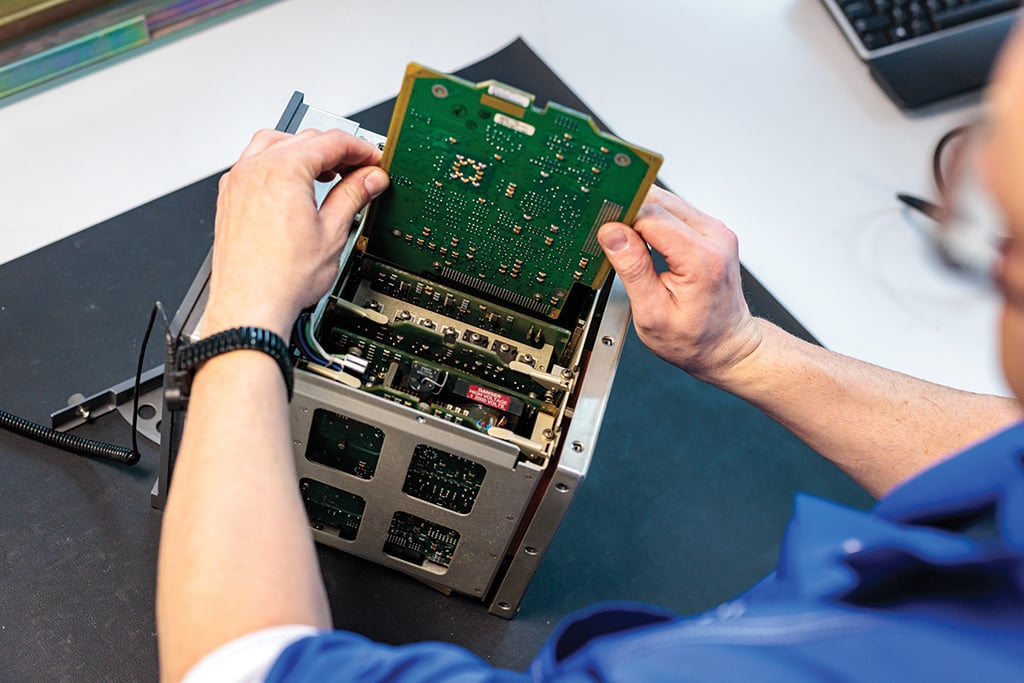
Van der Beek says FSG started a big continuous improvement program two years ago that is the foundation of these innovations, and the whole organization goes through Lean Six Sigma training. He notes FSG has a dedicated continuous improvement group, including rapid deployment teams for specific issues. FSG’s top priorities under this program have been improving turnaround times and on-time delivery.
“We hear from our customers that we indeed make a difference compared to others on turnaround time,” van der Beek says. “We have been able to pretty much sustain 10-20% of our standard [turnaround time], and that is because we provision more aggressively on these parts and we have invested in exchanges to support it. We have been very aggressive in recruitment of people and [keeping learning curves short], and all those things are also driven from the continuous improvement initiatives.”
FSG also receives more offload from OEMs, according to van der Beek. “We now see that we can get significant volume from certain OEMs to manage offload because they can guarantee our performance within that spectrum but still serve their own customers so they don’t lose them,” he says.
Digitalization and Workforce
FSG uses Pentagon 2000 and Veryon Tracking+ (formerly Rusada Envision) enterprise resource management software, and van der Beek says the company is working to create a suite of additional digital applications that can connect to these programs.
“We have an in-house development group that builds the software, advanced analytics, data factory platform, etc., and the intention is that within one or two years, we are digital in the hangar and in the workshop,” he says. “The biggest challenge is the connection between the systems, because no system is completely suitable to get a whole loop into digital, but we’re trying to make it happen.”
Van Dijk says FSG has observed the MRO industry’s workforce juniority challenge, but he sees an opportunity there with digitalization efforts. For instance, he says older, more experienced workers are often less inclined to use digital dashboards and prefer to print out documentation. “If we think about those new employees with a little bit less experience, they’re much more used to [technology] and it’s much easier to talk to them about it,” he says, noting opportunities to use emerging technology such as artificial intelligence.
FSG wants to continue growing its workforce and is involved with many technical schools, including one on-site at its Woensdrecht facility.
“We realize there’s no point in trying to get the next mechanic from KLM by offering €10 [($11)] more, because the next month KLM will offer €10 more, and we’ve got one employee going there,” van Dijk says. “The only way, longer-term, that we solve these issues is training the people and getting them interested in this industry. When I was growing up, being in the aerospace industry was kind of like the pinnacle that you could reach, and we believe that we should get that fight back.”